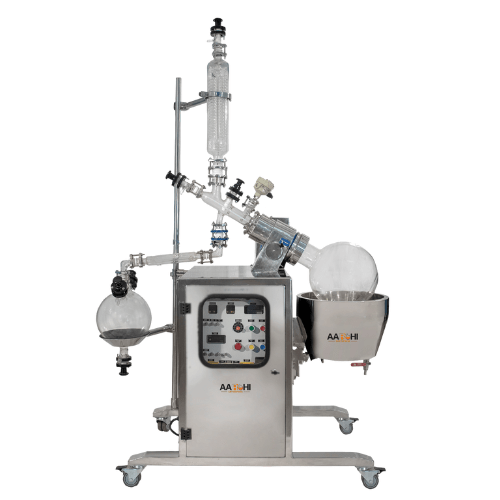
Introduction to Rotary Evaporator
Rotary evaporator, commonly referred to as “rotovaps,” are sophisticated laboratory instruments designed to remove solvents from samples efficiently. These devices have a historical lineage dating back to the mid-20th century when they were first developed to facilitate the rapid evaporation of solvents under reduced pressure. By utilizing a combination of vacuum, heat, and rotation, rotary evaporators significantly enhance the rate of solvent evaporation, making them indispensable in various scientific settings.
The primary purpose of a rotary evaporator is to separate solvents from solutes, enabling researchers to concentrate or purify substances. This functionality is particularly critical in fields such as chemistry and biology, where precise sample preparation is essential for subsequent analyses and experiments. The basic working principle involves heating a sample in a rotating flask, which is then subjected to reduced pressure. This setup promotes the rapid evaporation of the solvent, which is subsequently condensed and collected, leaving behind the solute.
Rotary evaporators are essential tools in both academic research and industrial applications. In organic chemistry, for instance, they play a crucial role in the synthesis and purification of compounds. In the field of biology, rotary evaporators are often used to concentrate biological samples, including DNA, proteins, and other biomolecules. Their versatility extends to environmental science, where they help in analyzing pollutants and contaminants.
The efficiency and reliability of rotary evaporators stem from their ability to control critical parameters such as temperature, rotation speed, and vacuum level. These parameters can be fine-tuned to optimize the evaporation process for different types of solvents and samples. As a result, rotary evaporators have become a cornerstone of modern laboratory practices, streamlined workflows and improved accuracy of experimental outcomes.
Components and Design
A rotary evaporator, often referred to as a rotovap, is an essential device in chemical laboratories for efficient and gentle removal of solvents. It comprises several integral components that work in unison to achieve this purpose. Understanding these components and their design is crucial for anyone looking to operate or comprehend the functionality of a rotary evaporator.
The primary component is the rotary motor, which serves to rotate the evaporation flask. This rotation increases the surface area of the liquid, promoting faster evaporation. The rotation also helps distribute the heat evenly, preventing local overheating and ensuring uniform evaporation of the solvent.
The evaporation flask is another key element, typically made of borosilicate glass, which holds the solvent to be evaporated. Its round-bottom design is optimal for efficient heat transfer and even distribution of the liquid during rotation. The flask is connected to the rotary motor and submersed partially in a heat bath.
The condenser is positioned above the evaporation flask and plays a pivotal role in the condensation of the evaporated solvent. It usually consists of a coil or a series of tubes through which coolant is circulated. As the solvent vapor passes through the condenser, it cools and condenses back into liquid form.
The condensed solvent is collected in the collection flask, located at the bottom of the condenser. This flask is also typically made of glass and is designed to easily remove and measure the collected solvent.
An integral part of the rotary evaporator system is the vacuum system. By reducing the pressure within the apparatus, the vacuum system lowers the boiling point of the solvent, allowing it to evaporate at a much lower temperature. This is particularly beneficial for heat-sensitive materials, as it prevents thermal decomposition.
Overall, the design and functionality of each component of a rotary evaporator are meticulously crafted to ensure efficient and safe solvent evaporation. Understanding these components not only aids in proper operation but also enhances the comprehension of the intricate processes that occur within the device.
Working Principle
The fundamental working principle of rotary evaporators revolves around the concepts of evaporation and condensation. At its core, the rotary evaporator is designed to facilitate the efficient separation of solvents from mixtures through the controlled application of heat and reduced pressure. By reducing the pressure within the system, the boiling point of the solvent is significantly lowered, enabling evaporation to occur at much lower temperatures than under normal atmospheric conditions. This is particularly advantageous for the evaporation of heat-sensitive substances, as it minimizes the risk of thermal degradation.
Temperature control plays a crucial role in the operation of rotary evaporators. A heated water or oil bath is commonly employed to provide a consistent and adjustable source of heat to the mixture contained within a rotating flask. The rotation of the flask is a key aspect of the process, as it increases the surface area for evaporation and promotes uniform heating. This rotational motion also helps to prevent bumping, a phenomenon where sudden boiling can cause the contents to splatter.
As the solvent evaporates, it is directed towards a condenser, where it encounters a cooling system, often utilizing circulating water or refrigerants. The vapors condense upon contact with the cooled surface and are collected in a separate receiving flask. This continuous cycle of evaporation and condensation under reduced pressure ensures efficient and rapid solvent removal.
The precision offered by rotary evaporators in terms of temperature and pressure control makes them indispensable tools in laboratories, particularly in chemical synthesis, pharmaceuticals, and food industries. By optimizing these parameters, researchers and technicians can achieve high-purity solvent separation, streamline workflows, and enhance the overall efficiency of their processes.
Applications in the Laboratory
Rotary evaporators, commonly referred to as rotovaps, are indispensable tools in both research and industrial laboratory settings. Their primary function is the efficient removal of solvents from samples through evaporation. This process is critical in various applications, allowing scientists and researchers to concentrate solutions, purify chemical compounds, and recover solvents with high precision and efficiency.
In the pharmaceutical industry, rotary evaporators play a crucial role in drug development and formulation. They are extensively used for the concentration of active pharmaceutical ingredients (APIs) and the removal of residual solvents from extracted compounds. This ensures the purity and efficacy of pharmaceutical products, meeting stringent regulatory standards. Moreover, rotovaps facilitate the isolation of natural products and the synthesis of new chemical entities, which are essential steps in pharmaceutical research and development.
The food and beverage industry also benefits significantly from the use of rotary evaporators. These devices are employed for flavor extraction, concentration of liquid extracts, and the removal of unwanted solvents from food products. For example, in the production of essential oils and natural flavorings, rotary evaporators enable the efficient concentration of volatile compounds, ensuring the preservation of delicate flavors and aromas. Additionally, in beverage production, rotovaps assist in the creation of extracts and concentrates that enhance the quality and consistency of the final product.
Environmental science laboratories utilize rotary evaporators for the analysis and purification of environmental samples. These devices are instrumental in concentrating pollutants from water, soil, and air samples, facilitating the detection and quantification of contaminants. This application is vital for environmental monitoring and regulatory compliance, ensuring that environmental standards are met and maintained.
Overall, the versatility of rotary evaporators makes them an essential component in various fields of scientific research and industrial applications. By enabling efficient solvent removal, concentration, and purification processes, rotovaps contribute significantly to advancements in pharmaceuticals, food and beverage production, and environmental science, among other disciplines.
Operational Procedure
To operate a rotary evaporator safely and effectively, it is essential to follow a systematic procedure. Begin by preparing the equipment and the materials. Ensure that the rotary evaporator is clean and free from any residues from previous operations. Check that all the necessary components – the condenser, evaporating flask, receiving flask, and vacuum pump – are in place and functioning correctly.
Next, pour the sample into the evaporating flask, making sure not to exceed the recommended volume to prevent spillage and ensure efficient evaporation. Secure the flask to the rotary evaporator using the appropriate clamp. Attach the condenser and the receiving flask, ensuring they are tightly sealed to prevent any leaks.
Adjust the temperature of the water bath to the desired setting based on the boiling point of the solvent you are evaporating. Typically, the temperature should be set 20-40 degrees Celsius below the solvent’s boiling point to ensure efficient evaporation without degradation of the sample. Turn on the rotary motor and set the rotation speed, usually between 50-200 RPM, depending on the viscosity of the sample.
Activate the vacuum pump to reduce the pressure inside the system. Lower pressure reduces the boiling point of the solvent, allowing for more efficient evaporation. Monitor the vacuum gauge to ensure it reaches the desired level. Keep in mind that tight seals and properly maintained equipment are crucial for maintaining a consistent vacuum.
During the evaporation process, continuously monitor the system. Observe the solvent condensation in the condenser and the collection in the receiving flask. Adjust the rotation speed, temperature, and vacuum as needed to maintain optimal conditions. If any issues arise, such as leaks or inadequate evaporation, troubleshoot by checking for loose connections, ensuring the vacuum pump is functioning correctly, and verifying the temperature settings.
Once the evaporation is complete, gradually release the vacuum to prevent sudden pressure changes. Turn off the rotary motor and carefully remove the evaporating flask. Collect your concentrated sample from the receiving flask, ensuring to handle it with care to avoid contamination.
By following these detailed operational steps, you can achieve consistent and reliable results when using a rotary evaporator, ensuring both safety and efficiency in your laboratory procedures.
Safety Considerations
When operating rotary evaporators, adhering to safety protocols is paramount to avoid potential hazards. The primary risks associated with these devices include chemical exposure, glassware breakage, and vacuum system failures. Understanding and mitigating these risks is critical for ensuring a safe laboratory environment.
One of the foremost concerns is chemical exposure. Rotary evaporators often handle volatile and hazardous substances. To minimize exposure, always use appropriate personal protective equipment (PPE), including lab coats, safety goggles, and chemical-resistant gloves. Additionally, working within a fume hood can further reduce the risk of inhaling harmful vapors.
Glassware breakage is another significant hazard. The glass components of a rotary evaporator, such as the evaporation flask and condenser, are fragile and can shatter under stress. To prevent breakage, inspect glassware for cracks or defects before use and handle all glass components with care. Using properly sized and compatible glassware can also minimize the risk of accidents.
Vacuum system failures pose additional risks, including the potential for implosions. Ensuring that the vacuum system is well-maintained and functioning correctly is crucial. Regularly check for leaks and ensure that all connections are secure. It is also advisable to use vacuum pumps equipped with an automatic shut-off feature to prevent system overpressure.
Safe handling of chemicals is integral to rotary evaporator operation. Always label chemical containers clearly and store incompatible substances separately. When transferring chemicals, use appropriate funneling techniques to avoid spills and splashes. In the event of a chemical spill, follow established emergency procedures, including evacuating the area and using spill kits to contain and neutralize the hazard.
Lastly, having a clear understanding of emergency procedures is essential. All laboratory personnel should be trained in first aid and emergency response, including the use of fire extinguishers and eyewash stations. Familiarize yourself with the location of safety equipment and ensure that emergency contact information is readily accessible.
Maintenance and Care
Proper maintenance and care of a rotary evaporator are crucial to ensure its longevity and optimal performance. Regular upkeep not only extends the lifespan of the equipment but also guarantees efficiency and safety during operation. One of the fundamental aspects of maintenance is cleaning. After each use, it is essential to thoroughly clean the evaporator’s components, including the evaporating flask, receiving flask, and the condenser. Use a mild detergent and warm water to remove any residues and prevent the buildup of materials that could impair functionality. Always ensure components are completely dry before reassembling to avoid any moisture-related issues.
Inspecting the components regularly is another critical practice. Pay close attention to the seals and gaskets, as they are prone to wear and tear. Damaged or worn-out seals can lead to leaks, which can compromise the vacuum efficiency and overall performance of the rotary evaporator. Replace any defective parts immediately, following the manufacturer’s guidelines for compatible replacements. Additionally, check the glassware for any cracks or chips and replace them if necessary to prevent accidents and ensure the integrity of the system.
Routine checks are imperative for maintaining the rotary evaporator in peak condition. Regularly examine the vacuum pump and ensure it is operating correctly. Monitor the system for any unusual noises or vibrations, which could indicate potential issues. Lubricate moving parts as recommended by the manufacturer to prevent friction and wear. It is also advisable to periodically calibrate the temperature and rotation settings to ensure accurate and consistent results.
Adhering to the manufacturer’s recommendations is paramount for maintenance. Each rotary evaporator model may have specific guidelines and maintenance schedules, which should be strictly followed. The manufacturer’s manual often provides detailed instructions on cleaning, inspection, and part replacement, tailored to the particular model. By following these guidelines, users can avoid common pitfalls and ensure their rotary evaporator remains in optimal working condition for years to come.
Recent Advances and Future Trends
Recent years have seen remarkable advancements in the technology underpinning rotary evaporators, transforming them into more efficient and user-friendly devices. One of the most significant innovations is the integration of digital controls. These systems provide precise monitoring and adjustment of parameters such as temperature, pressure, and rotational speed, enhancing the accuracy and reproducibility of experimental results. Digital interfaces also enable data logging and remote operation, which can be particularly beneficial in high-throughput laboratories.
Automation is another key trend in the evolution of rotary evaporators. Automated systems can now perform routine tasks such as solvent addition and removal, reducing the need for constant supervision and freeing up valuable time for researchers. These systems often include safety features such as automatic shut-off in case of overheating or vacuum failure, minimizing the risk of accidents. Enhanced safety protocols are increasingly standard, addressing concerns related to the handling of hazardous chemicals and high temperatures.
Improvements in efficiency are also noteworthy. Modern rotary evaporators are designed to achieve faster evaporation rates, thanks to advancements in condenser technology and vacuum pumps. These improvements not only speed up the evaporation process but also reduce energy consumption, aligning with the growing emphasis on sustainability in scientific research.
Looking to the future, several trends are poised to influence the development of rotary evaporators. The integration of artificial intelligence and machine learning could lead to smarter systems capable of optimizing evaporation processes in real-time. Additionally, the demand for miniaturized and portable units is likely to grow, driven by the need for on-site analysis in fields such as environmental monitoring and forensic science.
Overall, the future of rotary evaporators looks promising, with continuous innovations aimed at meeting the evolving needs of the scientific community. As these technologies advance, they will undoubtedly provide researchers with more powerful tools to accelerate their work and achieve new breakthroughs.